Comment réduire ses coûts de production grâce à la méthode SMED ?
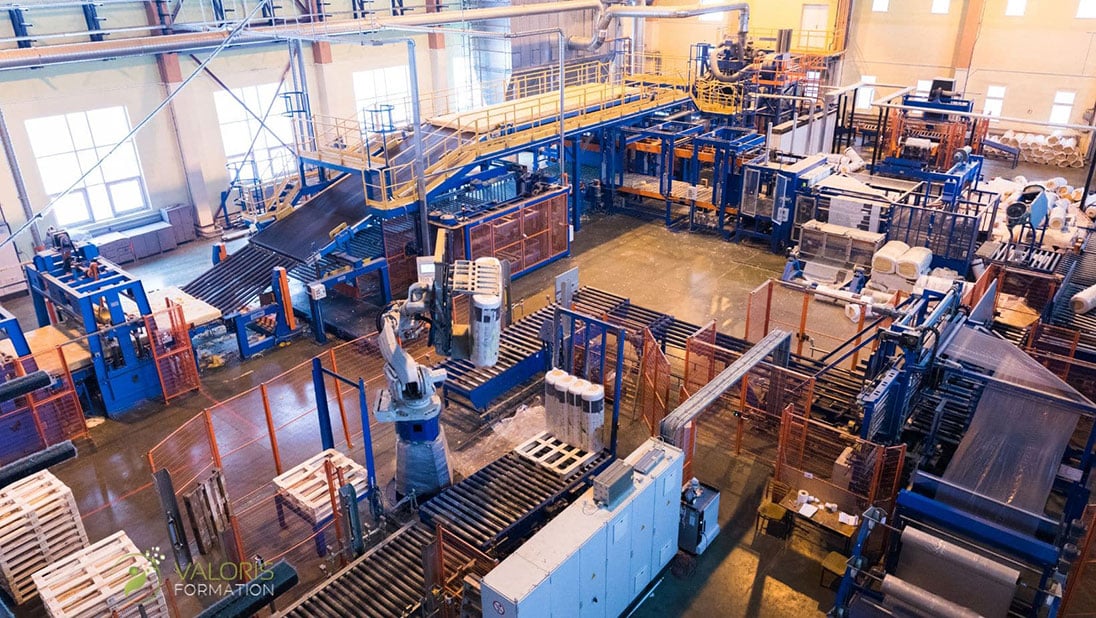
par Ninon
La méthode SMED, acronyme anglais de Single Minute Exchange of Die, est une technique de production développée par Shigeo Shingo, un ingénieur japonais reconnu pour son expertise en lean management. Cette méthode vise à réduire de manière significative les temps de changement de série dans les systèmes industriels. En optimisant les processus de production, les entreprises peuvent non seulement diminuer leurs coûts de fonctionnement, mais également améliorer leur flexibilité et leur compétitivité.
Cet article explore les principes de base de la méthode SMED, ses avantages et la procédure de mise en œuvre.
Comprendre la méthode SMED
La méthode SMED a été conçue dans les années 1950 au Japon par Shigeo Shingo, dans le cadre du système de production Toyota. Son objectif principal est de réduire les temps de changement d’outils afin d’augmenter la capacité de production tout en réduisant les coûts. Ce processus repose sur le principe que les changements rapides de série permettent une meilleure utilisation des équipements et une diminution des arrêts de production. L’enjeu est de transformer ces changements, souvent longs et complexes, en opérations simples réalisées en quelques minutes.
Le concept s’appuie sur trois principes fondamentaux :
- Tout d’abord, il est essentiel d’identifier et de regrouper les opérations internes (réalisées uniquement lorsque la machine est à l’arrêt) et les opérations externes (réalisables pendant que la machine est en fonctionnement).
- Ensuite, une partie des opérations internes doit être convertie en opérations externes, permettant ainsi de réduire le temps d’arrêt.
- Enfin, il convient de simplifier et de rationaliser toutes les opérations, grâce à des améliorations techniques ou organisationnelles.
Les avantages de la méthode SMED pour la réduction des coûts
1. Réduction des temps morts
En diminuant le temps total de changement de série, les entreprises augmentent leur productivité et optimisent l’utilisation de leurs machines. Les arrêts prolongés, souvent sources de pertes, sont ainsi évités, permettant une meilleure continuité de la fabrication.
2. Réduction des stocks
Avec des temps de changement raccourcis, il devient possible de travailler avec des tailles de lot réduites, favorisant une production en flux tendu. Cette approche diminue les besoins en stockage, les risques d’obsolescence et les coûts liés aux surfaces d’entreposage.
3. Amélioration de la qualité
La réduction des temps de réglage limite les erreurs humaines et matérielles. En assurant une meilleure précision lors des changements de série, les déchets sont réduits et la qualité des produits est renforcée.
4. Réduction des coûts opérationnels
Une mise en place efficace de la méthode SMED permet de réaliser des économies sur plusieurs niveaux : maintenance préventive, consommation énergétique, et optimisation du temps de travail des opérateurs.
La mise en œuvre pratique de la méthode SMED
La première étape consiste à analyser les processus existants pour identifier les goulots d’étranglement. Cela implique de mesurer le temps nécessaire à chaque opération et de déterminer les éléments qui peuvent être améliorés.
L’application de la méthode SMED repose sur une approche structurée. Tout d’abord, il faut distinguer les tâches internes et externes, puis convertir autant que possible les tâches internes en tâches externes. Ensuite, il convient de simplifier les étapes restantes grâce à l’élimination des actions superflues et à l’optimisation des outils et équipements. Par exemple, l’utilisation d’outillages standardisés ou de dispositifs de préparation peut significativement accélérer les changements.
La réussite de la démarche SMED repose sur l’implication des équipes. Former les opérateurs à chaque étape de la méthode permet non seulement de réduire les temps de changement, mais aussi de favoriser l’adhésion et l’engagement des collaborateurs. L’accompagnement par des experts peut également assurer un suivi rigoureux et durable des améliorations.
L’importance de la formation pour maîtriser la méthode SMED
Pour appliquer la méthode SMED de manière efficace, il est essentiel de suivre une formation SMED. Notre programme, conçu pour les responsables de production, les techniciens et les opérateurs, offre une méthodologie personnalisée et pratique.
- Objectifs pédagogiques : apprendre à réduire les temps de changement, augmenter la flexibilité et diminuer les coûts de production.
- Modalités : sessions de deux jours avec des exemples concrets, des études de cas, des travaux pratiques et des échanges d’expériences.
- Bénéfices : une meilleure compréhension des principes du lean management et une mise en œuvre efficace dans les environnements industriels.
La méthode SMED représente une approche structurée pour réduire les coûts de production tout en augmentant l’efficacité, la productivité et la qualité des produits. En appliquant ces principes, les entreprises peuvent non seulement optimiser leurs processus, mais aussi répondre plus rapidement aux demandes de leurs clients.
Passez à l’action en vous inscrivant à notre formation et
transformez votre industrie grâce à la méthode SMED.
Quelle GMAO choisir ?
29 octobre 2024
Comment faire une bonne maintenance préventive ?
11 juillet 2024